Groundbreaking Engineering with Swiss SLS 3D printer
At IMT, a Swiss engineering company, additive manufacturing methods have become an integral part of development. Among a variety of modern technologies, the team also uses a Sintratec S2 for faster iteration and verification of prototypes.
Innovation made in Switzerland
With around 100 engineers, Information Management Technology IMT headquartered in Buchs, Switzerland, is one of the major players on the Swiss engineering market. In recent years, the company has been particularly successful in the fields of medical technology and pneumatics. «Our core competence is the complete development of electronic devices with embedded software for industrial customers and especially for medical device manufacturers», says Benno Bieri, Chief Operating Officer of IMT. The company supports its customers from the initial idea with concept studies to the production-ready application and throughout the entire product life cycle.
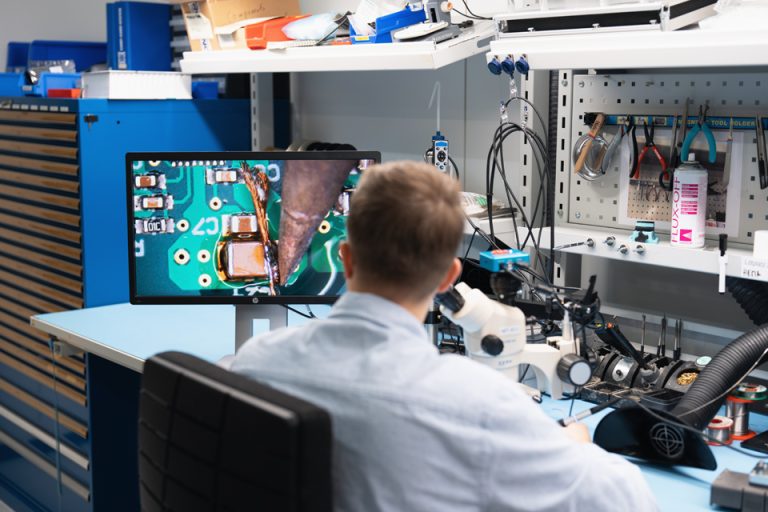
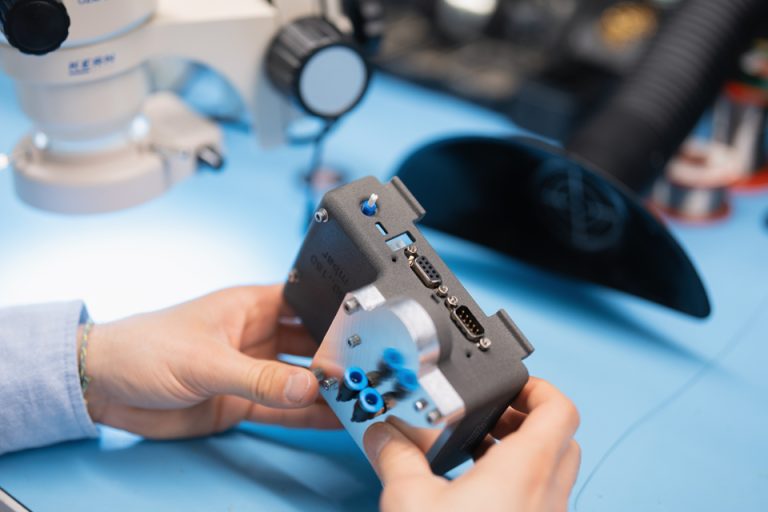
Around 100 engineers work on a wide range of development projects at the IMT headquarters in Buchs.
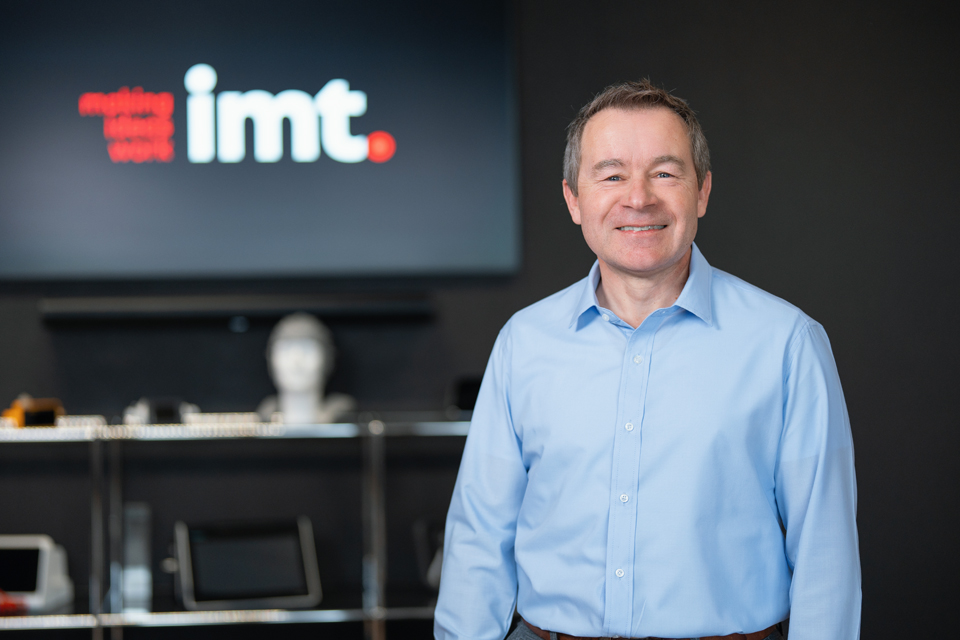
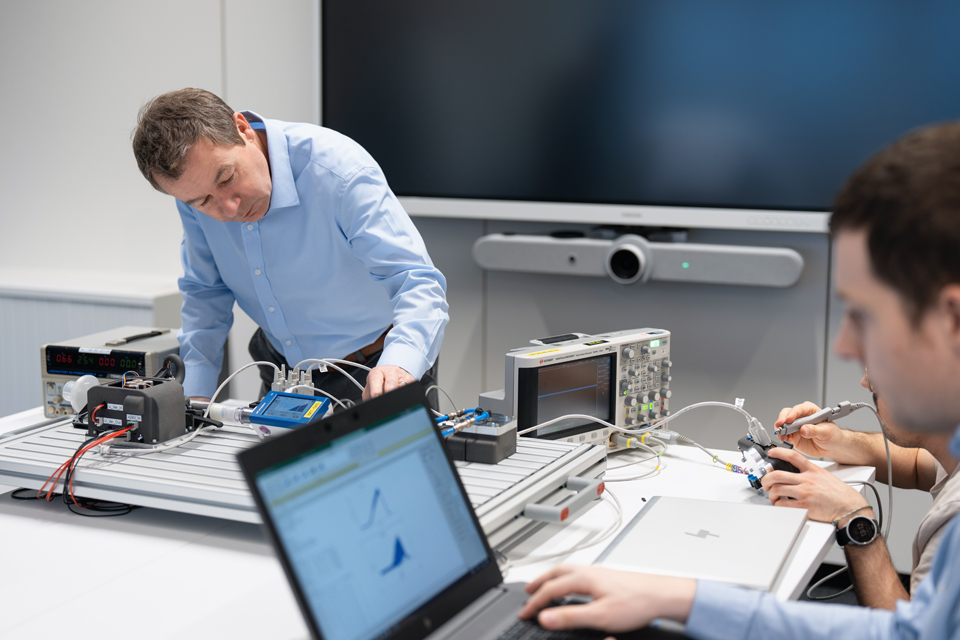
Embracing modern technologies
IMT’s credo is to be on the cutting edge of technology. A test laboratory with state-of-the-art equipment, for example for special environmental simulations, was just recently set up. Not surprisingly, the company has also been employing additive manufacturing processes for more than a decade. «We used to source 3D printed parts from external service providers», says Bieri. «Now we have several 3D printers in-house as demand has grown and we rely heavily on rapid iterations.» As customer requirements are becoming increasingly dynamic, these flexible technologies are needed more frequently and already in the early project phases.
Versatile manufacturing processes
Christoph Untersander is head of design at IMT and responsible for usability and prototyping. Together with the mechanical department, he uses various 3D printing processes to verify designs and simulations. Untersander explains: «Depending on the requirements we have for the part, we use appropriate technologies such as FDM (fused deposition modeling), SLA (stereolithography) or SLS (selective laser sintering).» Untersander’s team turns to SLS when the prototype needs to have isotropic – i.e. mechanically uniform – properties and an optically homogeneous surface.
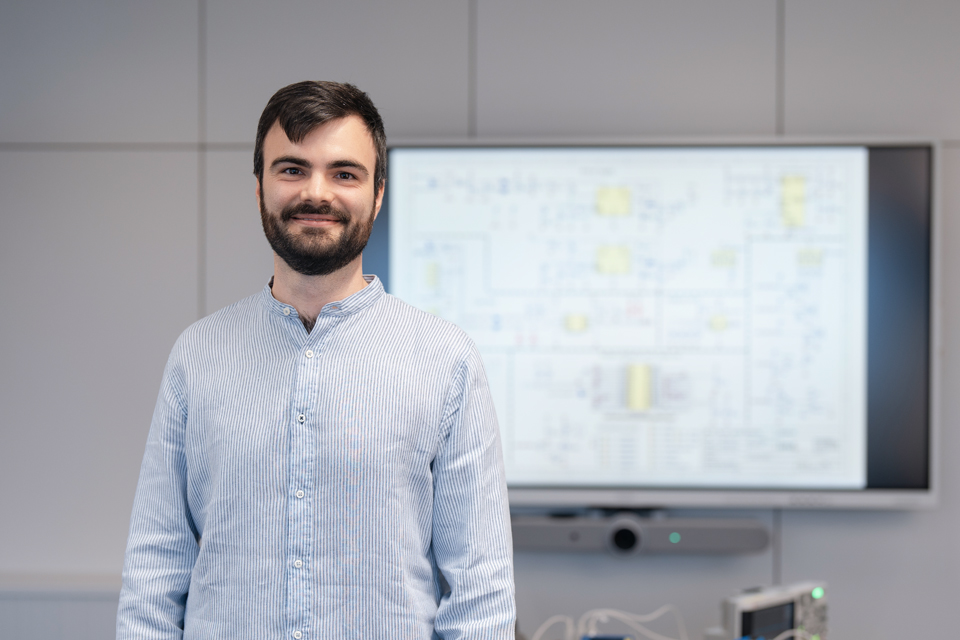
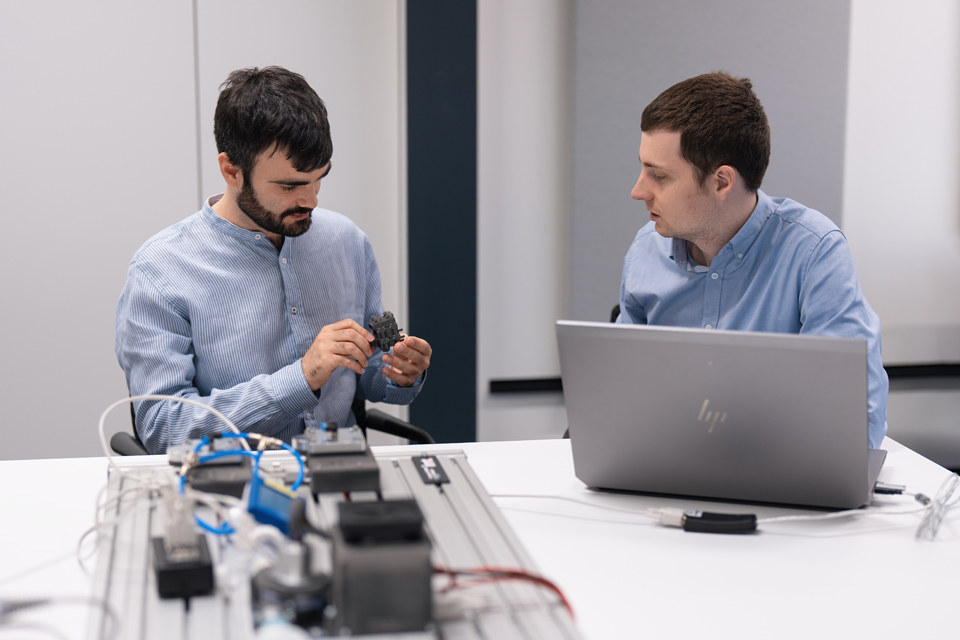
As Head of Design, Christoph Untersander often relies on 3D printing processes.
Swiss SLS 3D printer at work
A Sintratec S2 has been in use at IMT’s 3D printing center since late 2022. The engineers use it mainly to print prototype parts for internal development projects. For Vanessa Hug, designer at IMT, the SLS process offers clear advantages: «Because SLS does not require support structures, we are much freer in terms of design and can also create complex shapes», she explains. Hug is also responsible for operating the Swiss SLS 3D printer and supplying the other departments with the required parts. To that end, the designer relies on the PA12 material: «We use PA12 because it meets our requirements for accuracy, mechanical strength and gas tightness», says Hug. The latter is especially important for pneumatic applications.
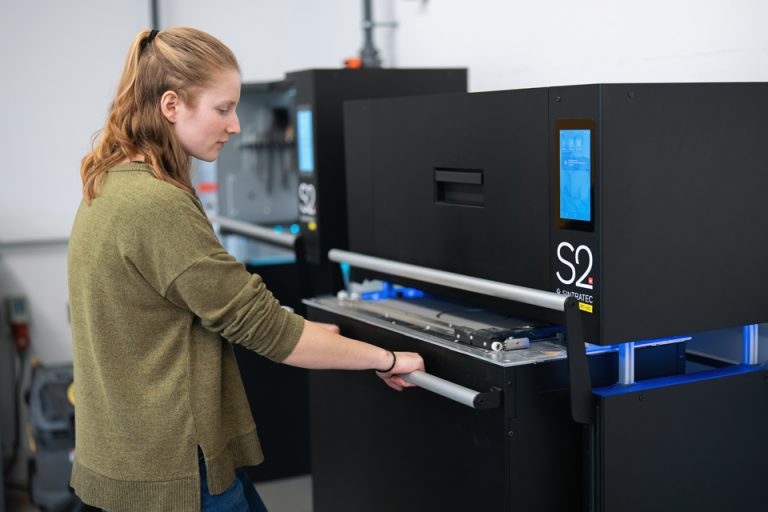
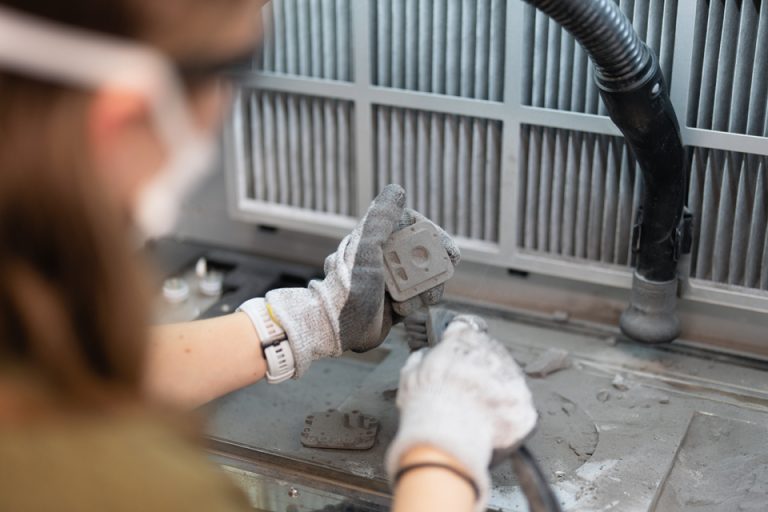
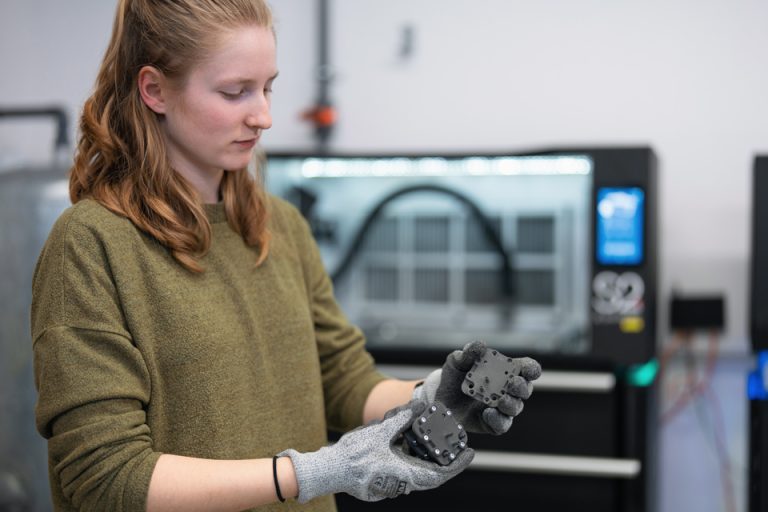
When precision and surface quality are important, designer Vanessa Hug produces parts with the Sintratec S2.
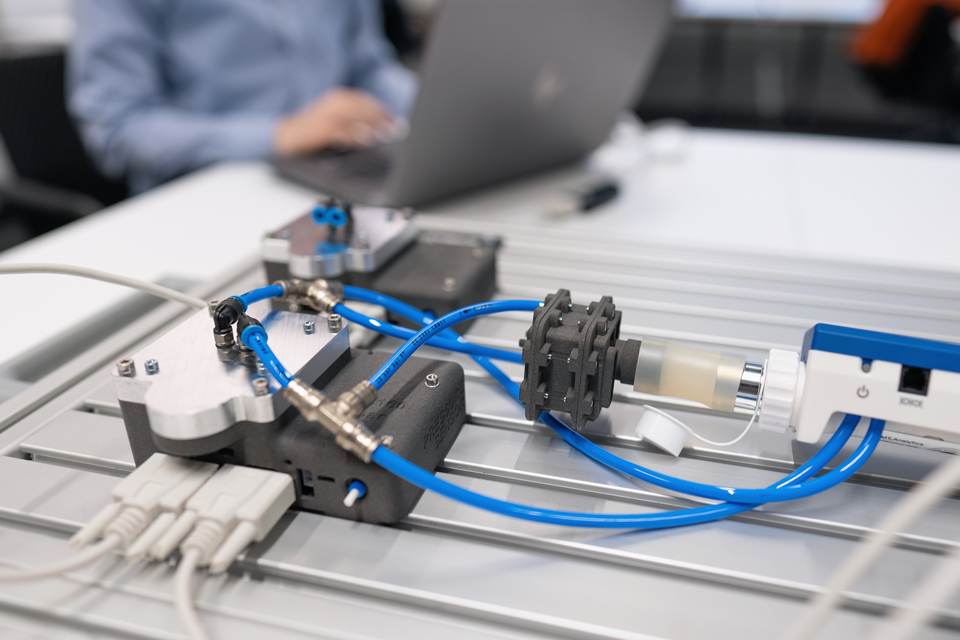
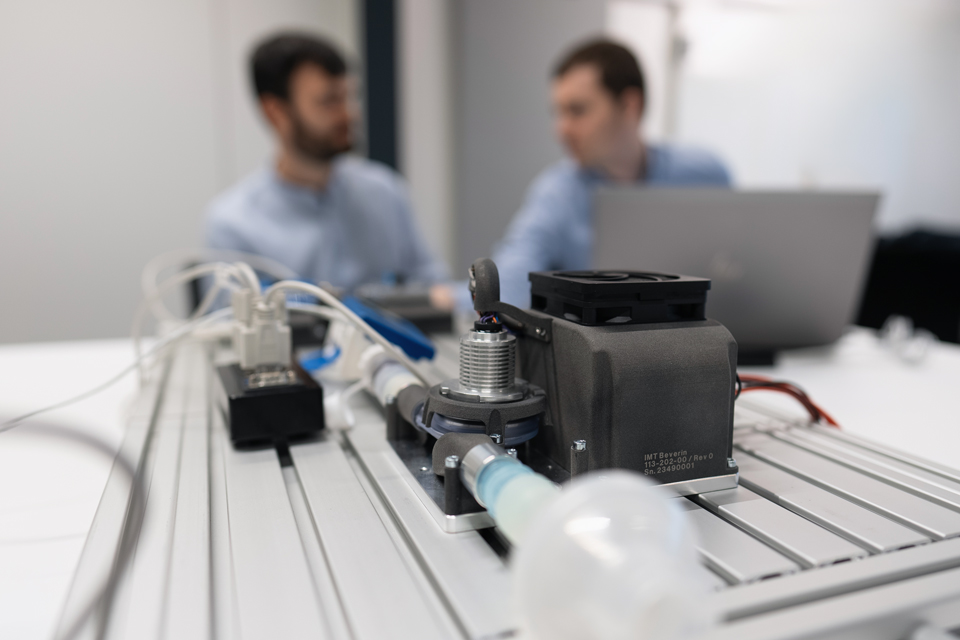
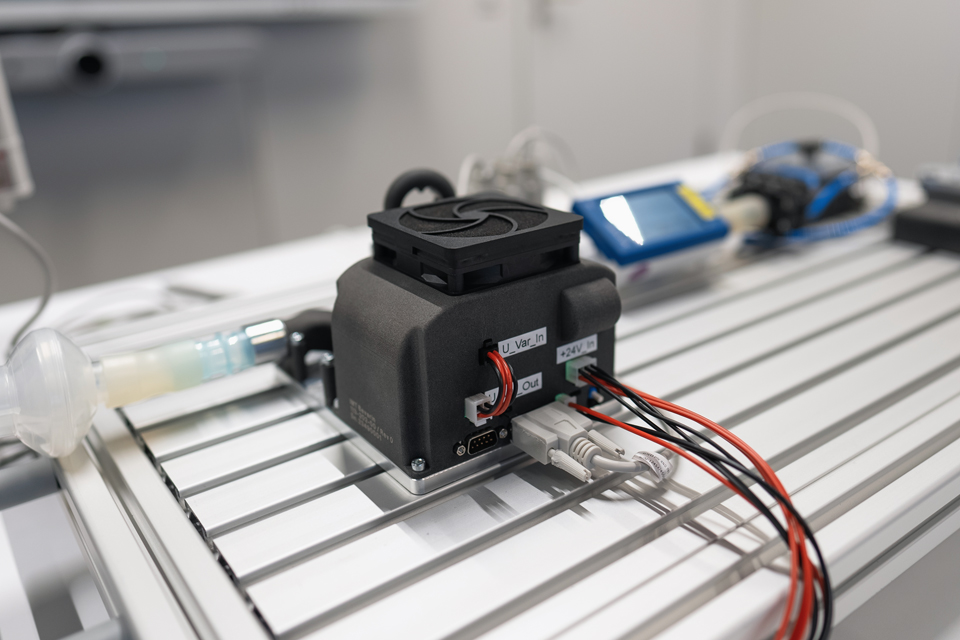
An internal test system contains numerous elements that were manufactured using the SLS process.
Covers, housings, complex parts
A specific application of additive technologies is the internal test system ‘Beverin’. The setup allows various components and sensors to be tested and measured on a modular basis. «For this test system, we manufacture numerous housings, cover elements and complex valves for gas flow measurement using the SLS process», explains Christoph Untersander. For these parts, dimensional accuracy in all directions and surface finish are particularly important to ensure that the end product is as close to reality as possible. Other 3D printing processes, such as FDM, would quickly reach their limits here.
Gas Flow Measurement with SLS
Christoph Untersander presents a part that is currently being verified on the test system: A complex valve for gas flow measurement. «After the simulation, we print a first prototype, which we install in our test environment and carry out measurements», he explains. «Then we measure the gas flow and try to optimize the geometry based on the sensor readings.» The design freedom of SLS enables construction approaches that would previously have been unthinkable. «And if there are adjustments, we’ll have the next part in our hands tomorrow», says Untersander.
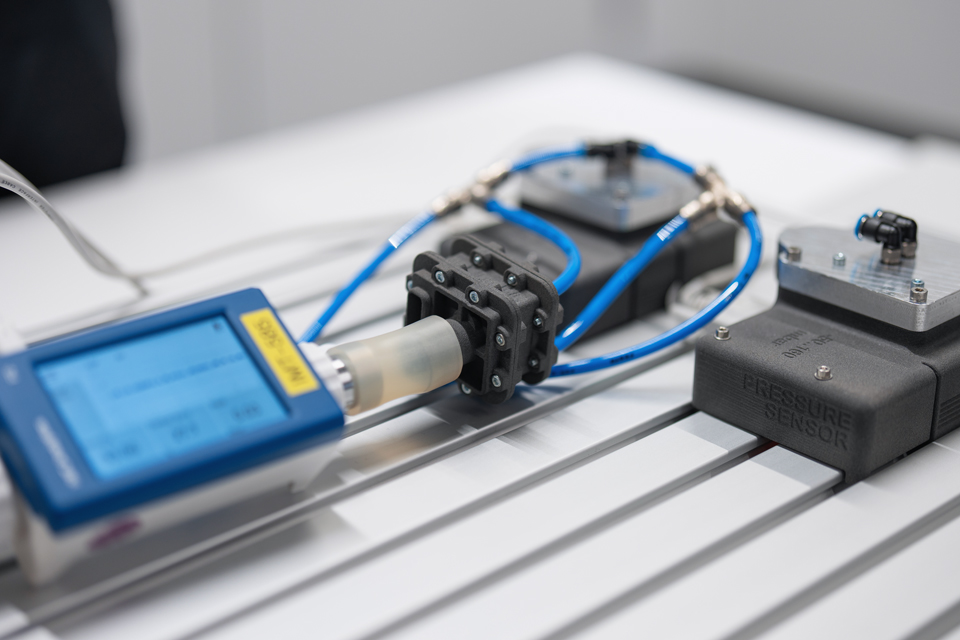
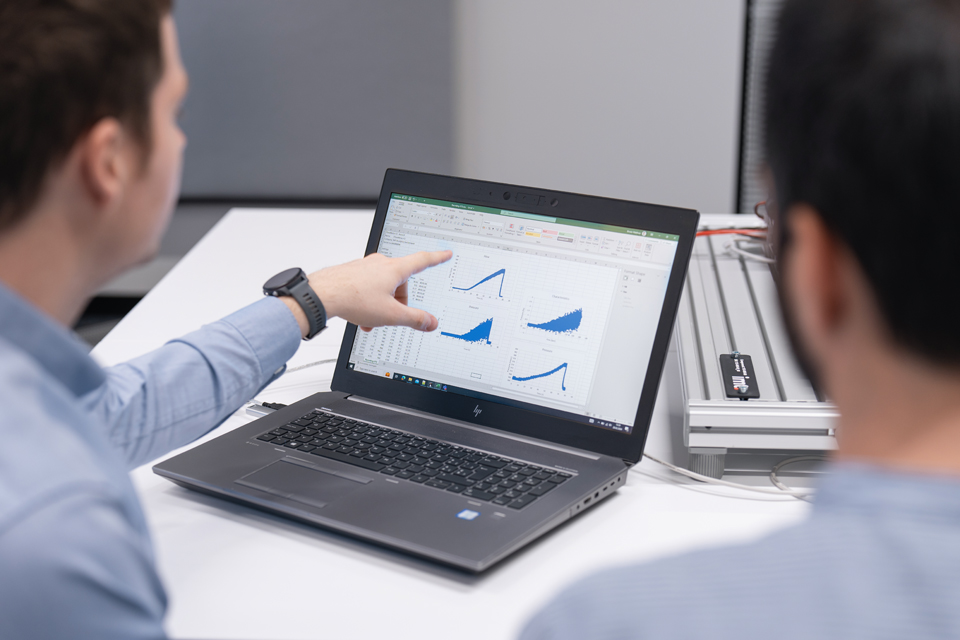
An SLS 3D printed valve is measured and its data evaluated.
Simulate – Test – Iterate
IMT development works according to the ‘Simulate – Test – Iterate principle. «Once we have met the specified criteria with the additive part, we can move one step closer to series production», says Untersander. The combination of virtual simulation, a realistic test situation, and rapid iteration has proven its worth to the engineering company. «This speed is particularly crucial, because every day saved is very valuable to us», emphasizes Benno Bieri. The next step will be to 3D print parts that cannot be produced in any other way in series. In Bieri’s opinion, additive technologies will continue to gain importance at IMT in the future.
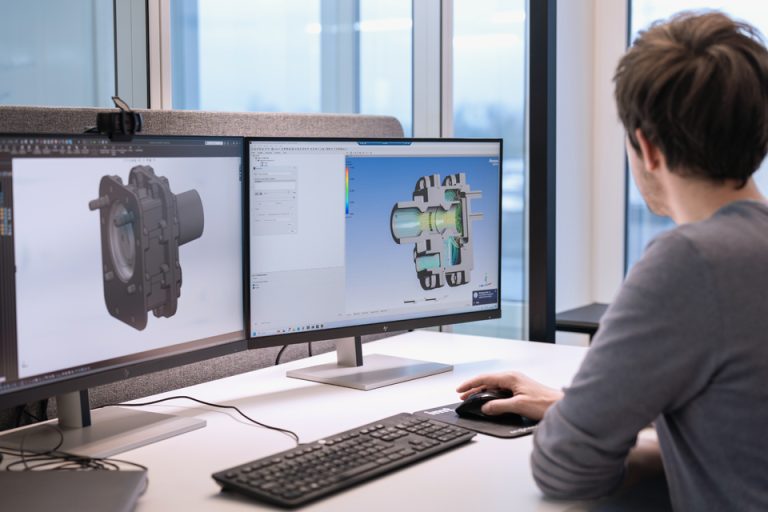
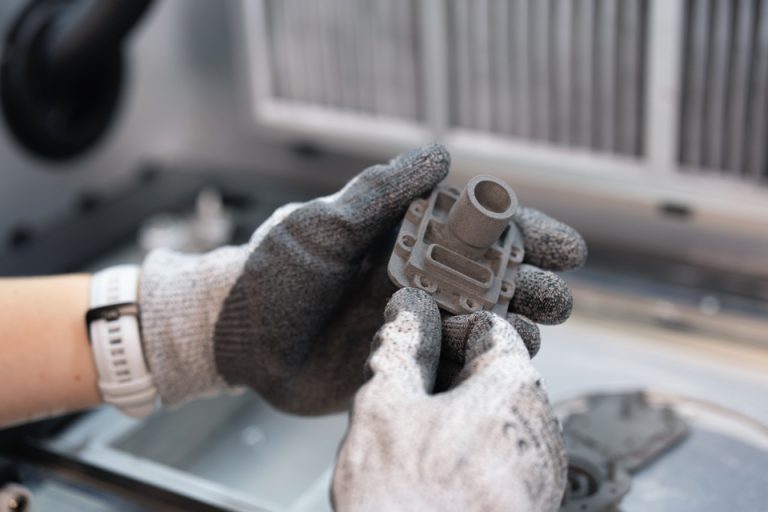
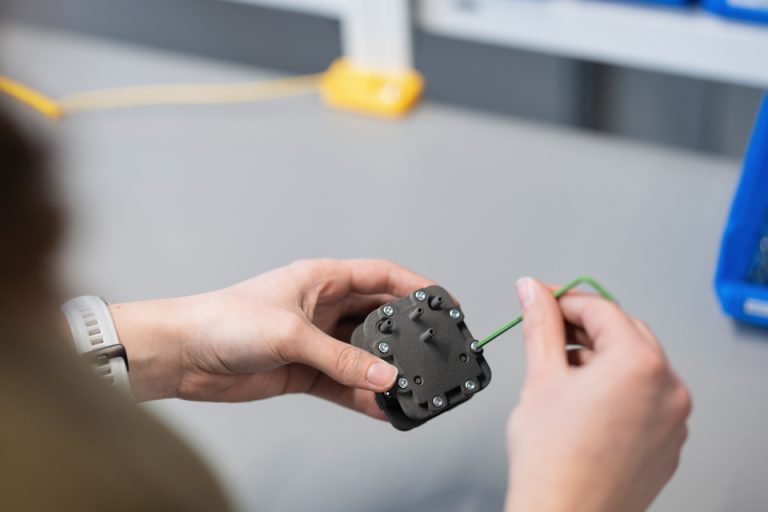
After simulation and testing, components can be rapidly optimized and iterated.
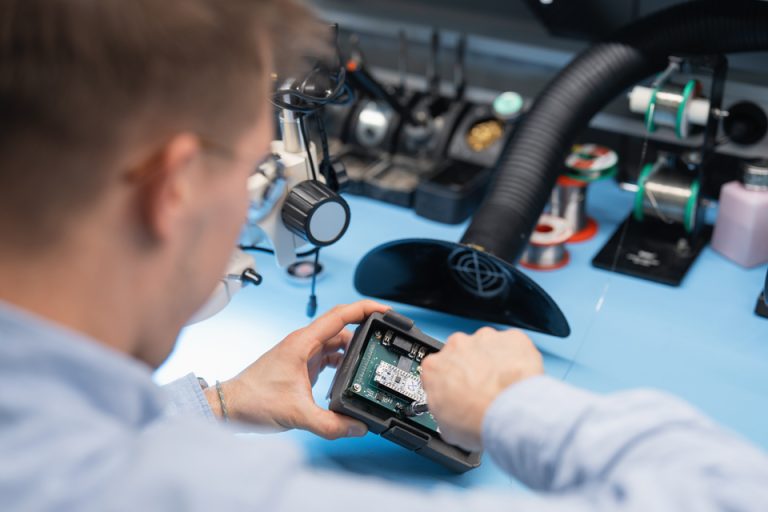
Proven Swissness
After more than a year and a half in use, the SLS process has become an integral part of research and development at IMT. It is no coincidence that a Swiss SLS 3D printer, in this case the S2, was chosen. «We really appreciate having Sintratec as a partner, a Swiss company with whom we can find solutions quickly and easily thanks to their proximity», summarizes Christoph Untersander. «In addition, we always get the highest quality from our Swiss partners», adds Benno Bieri. The use of the Sintratec S2 at IMT clearly demonstrates the contribution that modern 3D printing technologies can make to groundbreaking engineering.
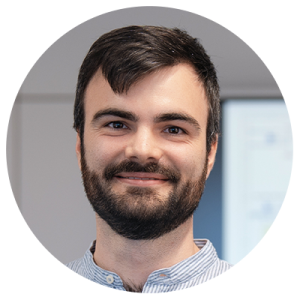
“With the Sintratec S2, we at IMT can produce complex prototype parts quickly and precisely, thus accelerating internal development projects.”
Christoph Untersander
Head of Design
IMT AG
Need consulting?
Our team is happy to advise you and to begin your journey into the world of SLS. Contact us right away!

[contact-form-7 id=”32022″ title=”Contact form Story”]