SLS 3D Printed Insoles – Redefining Podiatry
Mark Ireland has been successfully leveraging the capabilities of 3D printed insoles in his practice for almost three years. Utilizing the Swiss SLS 3D printer, the Sintratec S2, the podiatrist and his team have manufactured over 1300 pairs of their personalized 3D printed foot orthotics for their patients.
Pairs of Orthotics printed
PA12 Powder processed
Reduced Cost per Part
Patients treated with SLS
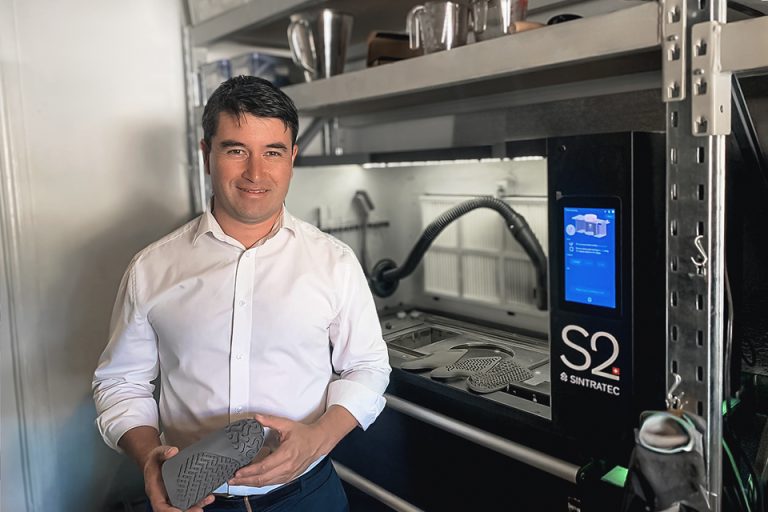
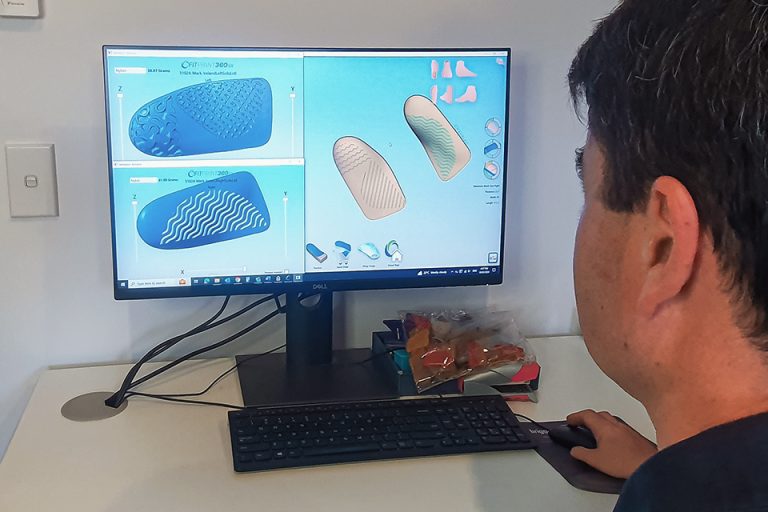
An industry on the rise
Advanced Family and Sports Podiatry (AFSP) from Albany, Australia, specializes in the treatment of foot and lower limb pain and dysfunction. We presented the modern practice back in 2021. Where does AFSP stand nearly three years later? «Things here Down Under have been extraordinary – the number of people seen at our practice has increased by about 30 percent», says Marc Ireland, owner and principal podiatrist. He attributes this success to the increased interest in personal health since the pandemic. As people take more care of their own fitness and lead more active lifestyles, there are also more injuries and wear and tear. «As a result, podiatry is needed more than ever to help people stay on their feet», Ireland notes.
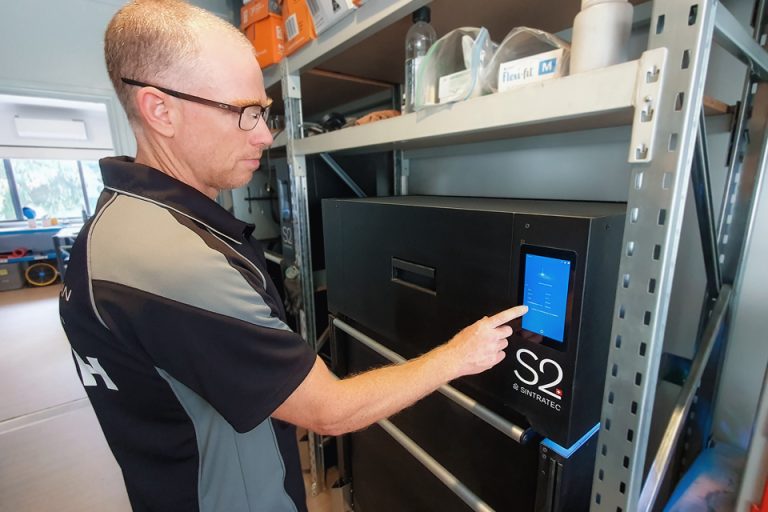
SLS 3D Printed Insoles
In early 2021, AFSP acquired a Sintratec S2. Since then, the team has been using the 3D printer in-house to provide patients with 3D printed insoles treatment within 24 hours. «With the S2, we have the ability to produce custom-fit insoles for the benefit of our patients – and in a turnaround time that cannot be achieved by outsourcing», Ireland emphasizes. The precision and design freedom of selective laser sintering (SLS) is also proving to be an important advantage over conventional manufacturing, where CNC milling was previously used. Mark Ireland explains: «If our patient’s foot has a deformity that could not be complemented with previous techniques, the S2 can rewrite what is possible.»
Efficient Production
Traditional manufacturing of orthotic insoles is time consuming and costly due to the number of steps involved. In contrast, additive manufacturing has become much more efficient. First, a 3D data model is created based on an individual foot scan and treadmill data in order to optimally adapt the orthoses to the person’s anatomy. Once converted into a 3D design, printing takes place on the powder-based Sintratec S2 system. To that end, Mark Ireland is using Sintratec PA12, a robust nylon material. «The lightness and durability of this material is unmatched by traditional methods», says the podiatrist. After printing and cleaning, the insoles are ready for use.
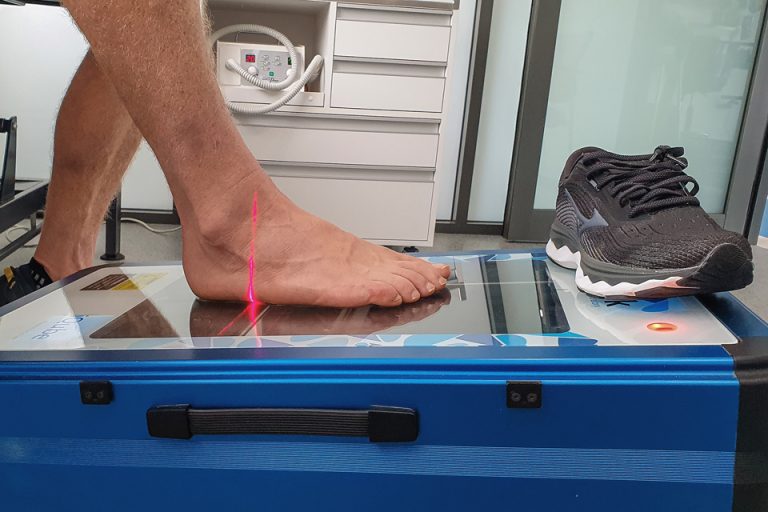
Important rethinking
For the team at AFSP, the Swiss 3D printer represented an important shift in thinking towards 3D printed insoles: “When we first started using the S2, we were probably doing orthotics that were more traditional in design,” explains Ireland. “But over time, we began to harness the performance of the material to produce devices that match feet and footwear more cohesively, providing a custom fit that improves the way the foot sits within the shoe.” These factors are particularly crucial for 3D printed medical aids in order to relieve painful areas or correct malpositions.
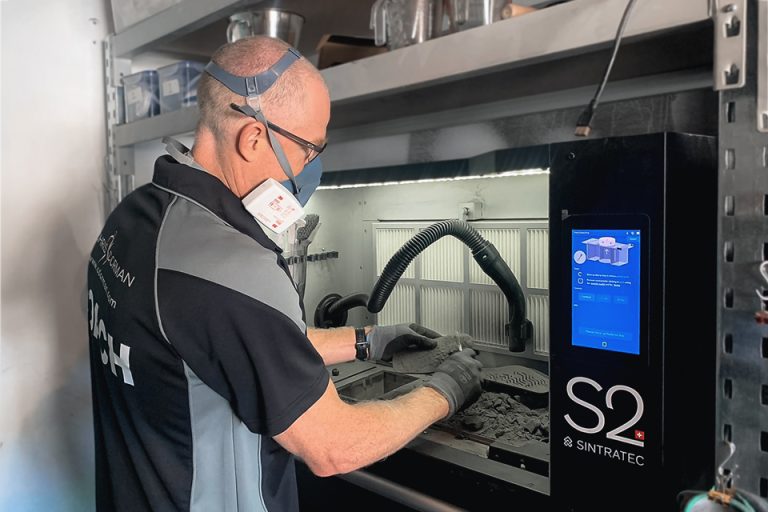
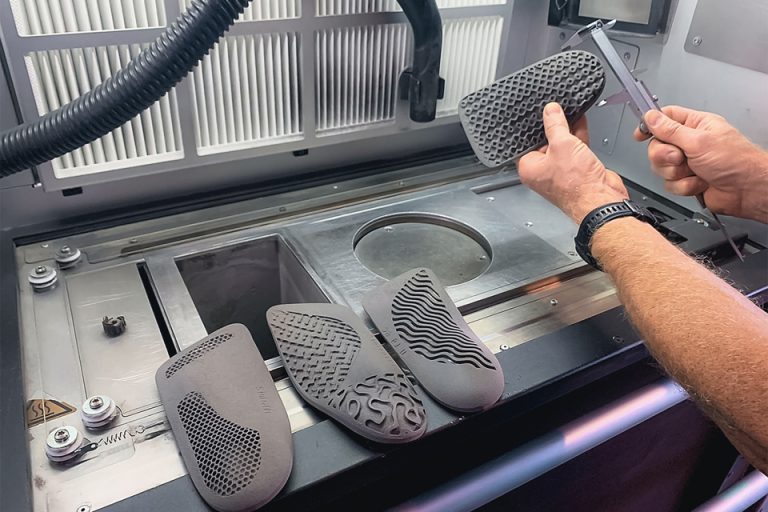
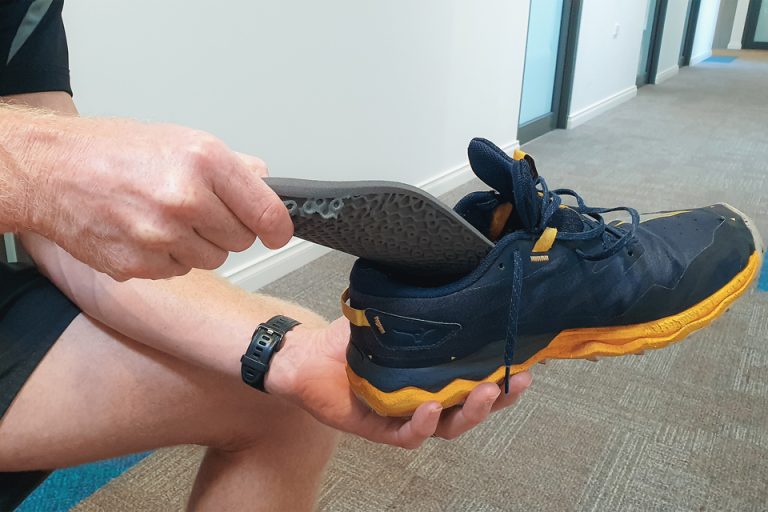
Versatile applications for lower limbs
However, AFSP is now using the 3D printing process to produce more than just foot orthotics. «We are now printing components that are specific to patient needs, including heel lifts, varus and valgus wedges, and we have even printed shoe raises that have been integrated into the midsole of footwear to help people with limb length differences», explains Mark Ireland. The lightweight yet stable structures can provide versatile support for the lower limbs. To date, more than 1500 patients have already been fitted with 3D printed devices by Mark Ireland and his team.
Reliable manufacturing tool
As the Australian practice grew, production volumes had to keep pace. «Our production of custom 3d printed foot orthotics using the S2 has increased every year since the introduction of the machine», says Ireland. Today, the printer runs almost every day. The throughput is emblematic of the success of the Sintratec technology in podiatry: more than 1300 pairs of orthotics have been manufactured and around 500 kg of PA12 powder has been processed since commissioning. Selective laser sintering is particularly suitable for the application, as no support structures are required and up to 8 pairs of insoles can be printed simultaneously in case of the S2. Compared to outsourcing, this results in cost savings of approximately 25%.
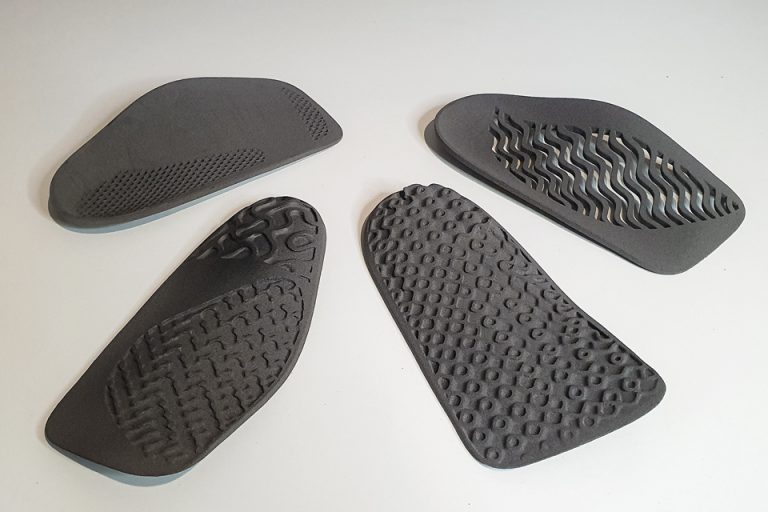
Successful pioneering work
It is evident that AFSP’s growth would not have been possible without the S2. “The performance, quality, and reliability of the Sintratec S2 has opened up our world for helping patients in a way that we could never have dreamed of,” Ireland exclaims. “The system has been a fundamental driver of our success and has created a unique service that only we can offer to our customers,” concludes the podiatrist. Accordingly, the practice is looking forward to an exciting future with the in-house S2. Today, personalized foot care in Western Australia has already reached a new level of quality thanks to the innovative pioneering work of Mark Ireland’s team with 3D printed insoles.
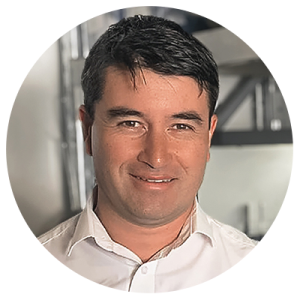
“The potential of the Sintratec technology is enormous in the podiatric field and should be a serious consideration for a podiatry practice.”
Mark Ireland
Owner and principal podiatrist
Advanced Family and Sports Podiatry
Need consulting?
Our team is happy to advise you and to begin your journey into the world of SLS. Contact us right away!
